
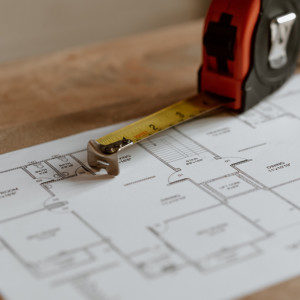
Estimating
Public Group
Public Group
Active 2 days ago
Estimating could include material take-offs for simple quantities or complex pricing. Whether you... View more
Public Group
How close is “close enough”?
Tagged: quantities, Rounding, takeoff, Tolerance
-
How close is “close enough”?
Posted by David Cutler on November 14, 2022 at 4:12 pmI’ve been working on this question in my mind for a while. How close is “close enough” in your takeoff world? We typically round our quantities to, at a minimum, the nearest full “unit” – SF, SY, CY, Ton, Etc. Sometimes – earthwork for example, we will round up to the nearest 100 CY. When capturing pavement quantities I don’t cut out around inlets and manholes for example.
How close is close enough for you and your industry?
Vince replied 2 years, 9 months ago 5 Members · 9 Replies -
9 Replies
-
Points: 16,958Rank: UC2 Brainery Advanced Blue Belt I
Excellent question David.
I’ve always looked at it like this, if I can’t have the exact quantity in there, then I can at least have the money in there.
There are some things though in Millwork where we really have to be careful. There are a lot of limitations to our products because of various material size limitations. Sometimes a simple square foot takeoff is off because you can only get the material in 4 x 8 sheets. You might have taken off 40 odd square feet, but you need to order 64 sqft, and you need to charge for that accordingly. GC’s and designers also don’t like seeing 35% waste.
I take off panel sizes all the time that make material yield horrible, 25″ wide panels, 19″ wide panels, 100″ long panels… you’d be stunned at just how many designers out there think that there are no limitations on material sizes. With any luck you can get that 25″ panel AND that 19″ panel out of the same sheet, but only if it doesn’t need to be sequenced matched.
Another big one for us right now is meeting NAWWS standards. Architects and designers seem think that wood grows perfectly straight, without any pin knots or sapwood. That we can get 16/4 QS walnut in 15′ lengths. When we tell them we can’t get that, they honestly freak out. Mills generally don’t even produce 16/4 in a Quarter Sawn material.When we’re doing a takeoff for these materials, we almost have to allow for 3 to 4 times the amount of material we’re going to used to meet the grade, or we have to allow for the money… which turns the board footage cost of 4/4 walnut from $11.50 bdft to $46 per bdft, because we need to buy 4 times the amount to meet their requirements. Don’t even get me started on FSC requirements… lol.
We do our level best to get it right, but this is estimating not accurating, we can only do so much.
-
Points: 29,759Rank: UC2 Brainery Advanced Brown Belt II
Always interesting to hear about the issues in other portions of the industry @Doug McLean
Do you make your allowances for waste? In your takeoff, in your data washing, or in your estimating system?
For example we measure storm drain piping from the center of the drainage inlet to the center of the next drainage structure. We then total all of the takeoff for a certain size – 18″ High Density Polyethene Pipe (HDPE) and enter that into our estimating software. Once it is entered – say 950 LF, we use that quantity for calculating our production. For purchasing we calculate and apply a waste factor so that we purchase 960 lf as the standard stick of pipe is 20 ft long. This can throw off your “typical” unit prices if say you are pricing a 22 ft long run as now you have 40 ft of pipe material cost in your item. Buying 2,000 lf for a 1,996 lf long run not so much.
Curb we run our takeoff and typically round up to the nearest 5 ft when we enter the item into the software.
Stone/Asphalt we typically round to the nearest 5 square yards.
Curious to learn how others handle this.
-
Points: 16,958Rank: UC2 Brainery Advanced Blue Belt I
Depends.
Our estimating software allows for us to set a waste percentage, so in most cases we’ll just do it that way.
But if its for something that I know I have a material limitation to, I do it in my markups. This is a great use for the Sketch to Scale markup tools and/or the alignment tools. I can lay out something evenly using a few lines and the ‘Distribute’ tools then place my markups accordingly. This way I can get an accurate sheet count as opposed to just square footage. Then when it imports into our estimating software the panel sizes are already accounted for.If its something like moulding, we’ll round up to the nearest length of whatever we’re shipping.
-
Points: 26,014Rank: UC2 Brainery Advanced Brown Belt
@David Cutler I’ve built tools for siding trim where I round each run to the next 12′ so we’re always using full-length pieces. this way my total is a reflection of each instance being rounded, rather than just the rounded total. This might generate more waste in this case, but in reality, the installers are not rummaging around the ground looking for a scrap that fits. Just a different approach to think about.
-
Points: 29,759Rank: UC2 Brainery Advanced Brown Belt II
I like the concept of rounding each piece @troy-degroot . I think I’d want to have a total both ways (straight measurement and rounded) so I would be able to better understand the waste that is being incorporated with the rounding. One could even incorporate a simple formula to calculate the waste in each run so you could avoid “over compensating”.
For example if you had 4 each 25 foot runs (100 lf neat length) you wouldn’t want to buy 2 each 20 ft sticks for each run (160 lf of pipe) as you would most likely have an extra 40 lf (or more) left over. At the same time I don’t know that I’d order exactly 100 lf either!
The other example would be 4 each 35 foot runs (140 lf neat length). I don’t think my superintendent would be happy if I ordered exactly 7 sticks and told him he had to use a bunch of 5 ft cutoffs to finish the last run. Here I probably would want 2 each 20 ft sticks per run so I’d order 160 lf.
Great discussion!
-
-
-
-
Points: 15,102Rank: UC2 Brainery Advanced Blue Belt
If I’m measuring groundworks then I certainly don’t make deductions for manhole covers, etc.. If you start going into that sort of detail then I think you’d also need to start adding in extra costs for working around the manholes, temporary protection, etc..
Things like drive areas and paving slab paths are all measured as per the drawings. The rates that we apply will allow for wastage. However, if someone designs a path at 1m wide using 0.60m wide paving slabs then we will increase the wastage factor significantly or possibly even measure the path as 1.20m wide.
Brickwork to houses is measured with the doors and windows deducted although I do know some people that still measure this gross. My argument with that is the percentage area of openings can vary greatly – maybe between 13 and 25%. The type of bricks or blocks is the thing that can have a significant impact on the wastage allowed. Some cut very easily whereas other (e.g. concrete bricks) have a tendency to shatter when they are cut.
Measuring roofing members is very different though. I will measure each individual rafter to the correct length then apply an allowance for cuts. The result is then rounded up to the nearest 300mm as this is the stage in which the standard lengths increase.
-
Points: 5,771Rank: UC2 Brainery Purple Belt
This is an interesting topic. The major point I see is that there is a difference between estimating and project buy-out. While in the estimating function, You are most likely bidding against other bidders and need to be careful not to bloat the pricing and lose out on the bid. It needs to be quick and efficient, adjusted for market conditions, completed and forgotten about so you can concentrate on the next bid. There is art to it.
Once the bid is awarded, the buy-out guys can worry about efficient material purchases, that’s their job. They can buy over multiple jobs, buy in bulk, ect.
Just my two cents.
-
Points: 29,759Rank: UC2 Brainery Advanced Brown Belt II
Great points @dhwalkellc – especially on the difference between estimating and buying out a project. Every industry, and company within that industry, have their approaches. Definitely interesting to hear everyone’s approaches.
-
-
Points: 15,102Rank: UC2 Brainery Advanced Blue Belt
@David Cutler I think the discussion is showing that there is a bit of a distinction between measuring internal or finishing items compared to civil works which is mainly due to the sizing of the products used.
Log in to reply.