
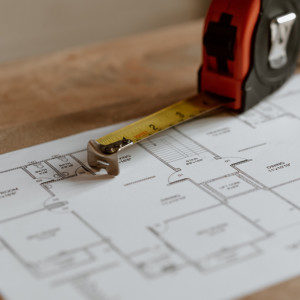
Estimating
Public Group
Public Group
Active a day ago
Estimating could include material take-offs for simple quantities or complex pricing. Whether you... View more
Public Group
Who wants to have some fun??
-
Who wants to have some fun??
Posted by Doug McLean on February 9, 2023 at 5:21 pmI thought I’d share what I’m working on in case someone wants to have a little fun.
Attached is a file of a set of Pod Seating elements in the project I’m currently working on.What we need to do is calculate the area of the diewalls that are on the outside edges of the Stair stringers, the area of the diewalls that are at the bleacher seating, AND the total area of the glass.
How would you do this??
Sorry about the redactions on the page, I have to keep this a little bit private… lol
Vince replied 2 years, 6 months ago 5 Members · 15 Replies -
15 Replies
-
Points: 17,120Rank: UC2 Brainery Advanced Blue Belt II
This is what the rendering looks like
-
Points: 4,958Rank: UC2 Brainery Orange Belt IIII
I have no idea how to do that, but this is a really cool space.
-
Points: 17,120Rank: UC2 Brainery Advanced Blue Belt II
About all I can say is that this is in a mall.
-
-
Points: 29,935Rank: UC2 Brainery Advanced Brown Belt II
I’m going to go back to measuring curb and sewer pipe for now. My head hurts just starting to think about how to go about this @Doug McLean !😲
I’d be curious at some point to learn how you handle was allowances on projects like this. I know in the past you have mentioned that the available sheet good size tends to drive the waste allowance. On a feature like this I could see the quantity of waste being higher than the quantity of useable material!
-
Points: 17,120Rank: UC2 Brainery Advanced Blue Belt II
Waste is a LOT higher. You start dealing with curved parallelograms
-
Points: 17,120Rank: UC2 Brainery Advanced Blue Belt II
The waste is really in the core, IF you do it properly.
We can lay out the core in such a manner that we can keep waste down, but that all does depend on the veneer species.
What we’ll do is lay out the veneer on the parallelogram, so when we bend it all lines up nicely.
-
-
-
Points: 15,219Rank: UC2 Brainery Advanced Blue Belt
@Doug I’m not 100% sure about this but here goes!
By the looks of it most of your shapes are circles so by using the change in height or the pitch, you can then work out the shape of the ellipse that is created on the angle.
With the two new radii you should be work out the perimeter of the new shape which can then be multiplied by the height.
You can test this with some sketch to scale shapes.
There are also a couple of ways of calculating the length in Excel depending on whether you have the height or pitch.
If you are only completing a wall to part of the perimeter then hopefully it is just a pro-rata calculation that needs doing.
Hopefully this works?????
It’s a bit hard to explain here so I’ve attached a couple of files.
-
Points: 26,297Rank: UC2 Brainery Advanced Brown Belt
This is awesome @Doug McLean
I’m curious if you used the polylength tool to trace the path of the radious, this would give you the length. Then take that length with the regular length tool and add the stair pitch. This should calulate the new length, then add the depth to get the wall area.
Pretty straight forward it you read that six times. 🤣
-
Points: 17,120Rank: UC2 Brainery Advanced Blue Belt II
We do seem to get the fun jobs at Towne Millwork…lol
Helical stairs give Revu fits.
You cannot take a Polylength tool, apply a curve, and then give it a slope. Revu won’t let you as it grey’s out the tool.
As a Joiner we learn how to do this math in the 3rd year of our Apprenticeship, so I know the math.
Luckily, I don’t have to figure out the total rise and total run because I can just take those measurements.
@Vince hit it dead on, because I’m using Excel to do all the math here.
I may post the finished marked up page later.
-
Points: 29,935Rank: UC2 Brainery Advanced Brown Belt II
Amazing stuff @Doug McLean ! I’m thinking that once you win the project we will need to arrange a visit to your fabrication facility for the “Unofficial UChapter2 Advisory Board” to see how it all comes together… 😎
-
Points: 17,120Rank: UC2 Brainery Advanced Blue Belt II
I’m sure we’ll be able to post pictures of this one as it will be in a public space
-
-
Points: 15,219Rank: UC2 Brainery Advanced Blue Belt
I just about remember having to learn all sorts of calculations when I was at college @Doug – the one that sticks out was working out the surface area of the top of a cone that has been sliced at an angle.
But that was about 30 years ago so the actual details behind everything were forgotten a very long time ago!
One interesting job I remember doing with my dad was a circular oast house roof – for every three rafters in the bottom half there were only two in the top half.
-
Points: 29,935Rank: UC2 Brainery Advanced Brown Belt II
I remember working on “geometric constructions” or something like that in High School drafting class @Vince . We had to draw all of the surfaces on paper, cut them out and assemble them into a 3D shape. What started out with a simple cubes and cylinders progressed to a cylinder cut at an angle. I think I might still be able to recreate it if I thought about it enough… So much easier to do with modern software! 😎
-
Points: 15,219Rank: UC2 Brainery Advanced Blue Belt
@David a few years ago we started a project that had gas dpc’s that were to be cut & placed in-situ. The went across the cavity wall and then dressed down 6″ of brickwork and then left with a lap across the floor for the gas membrane to be fixed to later on.
The rolls of dpc for the external walls were 700mm wide and those on the internal party walls were 900mm wide.
The ends of each length had to be cut in a particular way in order so when it was all folded and taped together, there were full overlaps. Internal and external corners had different cuts as did the ends of party walls, etc..
A 700mm wide roll that is approx 60′ long costs just under £200.
So, you can imagine that we didn’t want the guys on-site making mistakes – especially when the site consisted or nearly 500 houses.
My answer was to make some scale examples with paper in my office.
Once I got those to work I then went out to my garage and cut templates out of 3no 8’x4′ x 1/4″ sheets of ply. They were all numbered up with the order in which to do the cuts as well.
When I dropped the templates off to site I think some of the men thought I was a bit mad – they ended up being grateful in the end though!
-
-
-
Points: 17,120Rank: UC2 Brainery Advanced Blue Belt II
Doing a helix is one of the most challenging aspects of Millwork (or Architectural Metalwork).
Wood doesn’t like to twist. You can if you steam it, but even that posts its own challenges.Designers like to think that this stuff is easy, but its not. It’s also expensive, because it takes a skilled tradesman to actually pull this off.
Back in the day, they would just sketch this out, and then a Finish Carpenter would lay these out on site and just start making it happen. There are tricks to doing these things. In todays world, with having to submit shop drawings for everything and CNC’ing parts, it actually makes it a bit harder.
Revit, ArchiCAD, Soildworks… they’re all awesome, but people have to try and build this stuff that designers are coming up with. It’s fun, but also challenging at the same time
-
Log in to reply.