
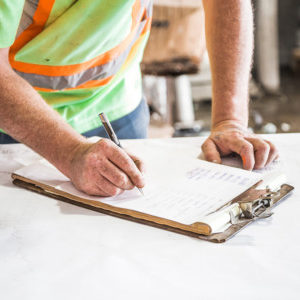
Punch Walk
Whether you’re doing As-Builts, tracking installation progress or performing a final walk-through, this... View more
Punch Process at the Start of a Project
-
Punch Process at the Start of a Project
A while back, it more or less dawned on me that the very beginning of generating an Estimate is essentially a Punch List.
You should try using these processes at the beginning, it works well.
Anyone else doing this?
Log in to reply.